Hot Rodding a Harman/Kardon T20 Part 1.
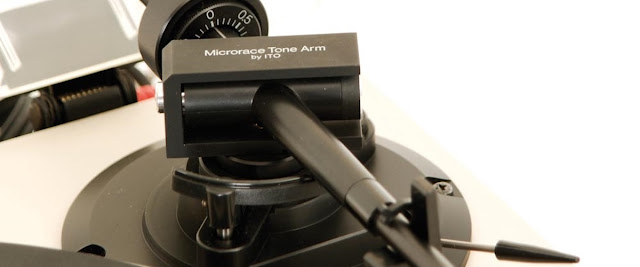
Do I need another turntable? No I already got too many. But I got that modding itch so why not another turntable? They are always fun to work on :)
There is nothing wrong with my daily driver, a Thorens TD-150. I bought it really cheap and in a horrible condition. I have since modded it with a new plinth in solid ash and a new bottom out of fairly thick MDF. The platter has been polished and the stock TP13a "Kugelarm" with its lovely headshell has been fully restored with NOS parts. This is like a poor mans Linn Sondek LP12 and it plays just as good.
But as much as I love this TT it lacks a dust cover and it is fully manual. I hate dust covers but they are convenient. I don't mind manual cuing but it would be nice with an auto off and tonearm lift (it is horrifying to wake up in the morning and find the platter still spinning with the stylus on the record, it doesn't happen often but it does happen).
So I was keeping my eyes open for a used TT with a small footprint like the TD-150. I usually only restore true classics but I wanted something that I could hot rod (without getting a bad conscience) this time. A stumbled upon a Harman/Kardon T20 on an auction site, it had the look I was looking for but was part of a greater lot that I was not interested in. I started to look for a T20 and found another one listed as broken/spare parts. What was important to me looked really good on picture, tonearm, platter, front panel and it even had a dust cover without any cracks. I ended up paying almost as much as I payed for the TD-150, or should I say even less?
Shipping a TT is always a bit of a gamble so I held my breath unpacking the beat up cardboard box. This one was nicely packed but what had I bought? I had only seen pictures of the H/K T20.
This TT has the clean look of a TT from the 80ths. It was the entry level of the H/K T20, T40 and T60 lineup. The build quality is a bit of a mixed bag. The low mass tonearm is nice. The front panel offers capacitance trim and frequency generator servo pitch control, witch is pretty impressive on an entry level TT. The platter is supposed to be high mass but it feels super light compared to the platter on my TD-150.
A wood base is supposed to be vibration absorbant in combination with rubber/coil spring suspension (more about it later). But I find the body to be a joke and easily the weakest link. This is the definition of entry level and cost saving. The "wood base" is made of thin MDF and strips of plywood, as can bee seen from underneath.
A lot of the mechanics are made out of brittle plastic with a cheap feel operating it, it is a petty. But vital parts like the platter bearing, motor and motor mount seems solid enough.
I was planning to make a new plinth and save the original one as I usually do (if I ever want to reverse a mod back to stock). But I will make an exception this time since I don't see this model ever turn into a classic worth keeping stock.
The bottom is just sad. It is made out of flimsy sheet metal. The grey stuff seems to be some sort of vibration dampening material. Each corner holds rubber/coil spring suspension feet.
These rubber/coil spring suspension feet is another joke, and broke (the main reason the TT was listed as broke/spair parts). Two in somewhat stock condition to the left and two totally bust to the right. Also the tiny M3 screws mounting them to the bottom plate. I really like that I got all four helix coils from the original feet. It makes it possible to make something new out of them in the future. But I got another idea initially but more about new feet in another post.
The TT came with a really nice cartridge, an Integra ST with a XLM-III stylus by ADC. If this one was in good condition it would easily pay for the the rest including mods. The stylus was bust unfortunately but the cartridge seems OK. So I will save it for the day I manage to find a new stylus (for a reasonable price).
I don't like the shape of the dust cover (the shape on the T40 and T60 is nicer) but it turned out quite OK after applying some elbow grease and Meguiar's ScratchX 2.0.
This is another stupid example of cheap over functional manufacturing. A micro switch was hold to this bracket by two M2.5 screws made out of brittle transparent plastic (one is snapped flush to the bracket, whats left of the other one is sticking up from the other hole). The micros switch had come loose making the semi-auto mechanism non functional.
My fix for this problem was quite simple. Re-drill the holes with a 2.5 mm bit and tap them with M3 threads. The micro switch can now be mounted with a pair of 12 mm M3 machine screws instead (as they should have been in the first place). They will never break like the plastic ones. Cost close to nothing so why the plastic ones? NOTE: I think I get the idea behind the skinny plastic screws. The service manual talks about adjusting the clearance. Maybe 2.5 mm gives a bit more play but I had no problem getting it right using my M3 screws.
Next problem was the phono cables. Here some little electrician been to work. I don't even know if I want to know whats under that tape?
I usually replace this kind of cables with custom made but I don't know if its worth the effort it in this case. Going through my "cable bin" I found this old A/V cable, perfect replacement for the stock one. Just use the video cable as the ground cable.
The cheaply made T20 doesn't encourage you to walk that extra mile and that is a bit sad. The T40 seems like a better built TT, heavier platter, disc stabilizer and a nice looking dust cover. The T60 seems really nice with all of the above plus a floating chassis and quartz lock. Well the T20 is what I got so I better make it work. More about it in my next post...